Furnace for Aluminium
Aluminium is the most commonly used non-ferrous metal today, other than iron. Aluminium resists corrosion more than most other metals. It is also prized for its reflective properties. Aluminium is a metal that is often recycled and reused, such as soft drink and beer cans. Aluminium is used in the transportation industry, aerospace industry, construction, household products of all kinds, electronics, packaging, electrical lines and even in paint, among many other applications. Because it is considered to be a lower density metal, the aluminium melting furnace is specifically designed for the purpose of melting aluminium. Lower density metals like aluminium require evenly distributed heat for melting, and the heat must be maintained at a precise temperature. Induction type aluminium melting furnace, utilizing an alternating current coil (electromagnetic induction) to melt the aluminium. Water is used as a coolant for the system.
This type of melting furnace is much more capable than others of producing the even and precise temperatures necessary for processing aluminium. In an induction melting furnace the action of the electromagnetic field actually stirs the aluminium as it melts, allowing the aluminium to maintain its integrity. Any impurities will rise to the top when melted and the pure aluminium will sink to the bottom.
The aluminium melting furnace is clean (non-polluting), energy-efficient, easy to control and can melt aluminium quickly. Induction furnaces in general are far less expensive to the operating and maintenance budgets, as well.
When selecting your aluminium melting furnace, you have several factors to consider relating to the furnace specifications, and depending on the volume of material to be processed and produced. These factors include:
We work closely with you to determine the precise requirements of your facility, and then create a custom solution for any requirement. We supply induction heating and hardening equipment for a wide range of industries, including:
- Melting Rate which refers to the amount of aluminium to be melted within a specific time period.
- Utilization Factor refers to the amount of time involved in any action which is not melting.
- Furnace Yield is the amount of molten metal which can be expected to be obtained in a certain time period after taking into consideration the utilization factor.
- Casting Yield refers to the amount of the final cast product. In order to determine this figure losses from pouring and moulding must be taken into account in order to determine the amount of aluminium to be melted to achieve the required amount of finished product.
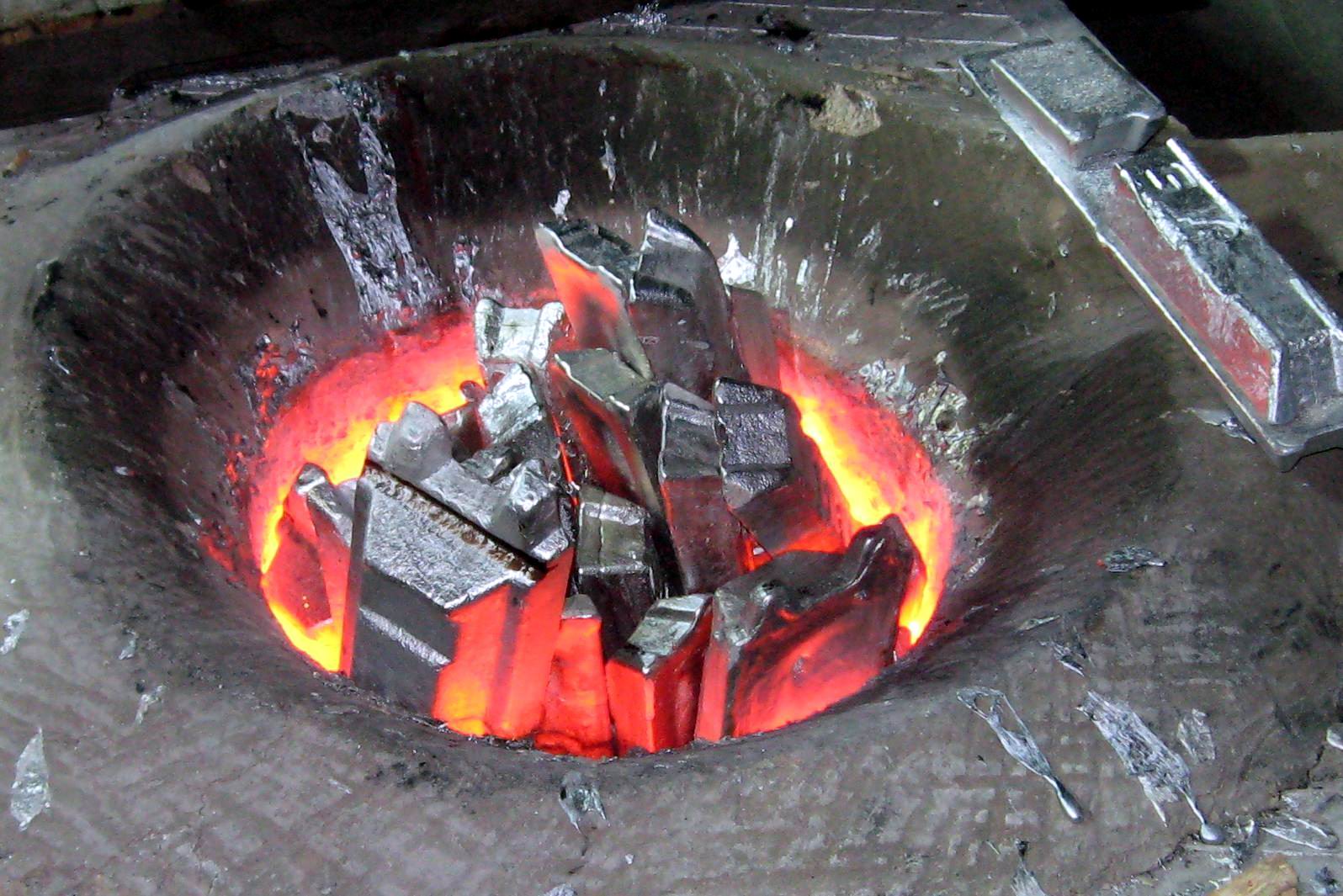